Rubber Moulded Collets In Oragadam
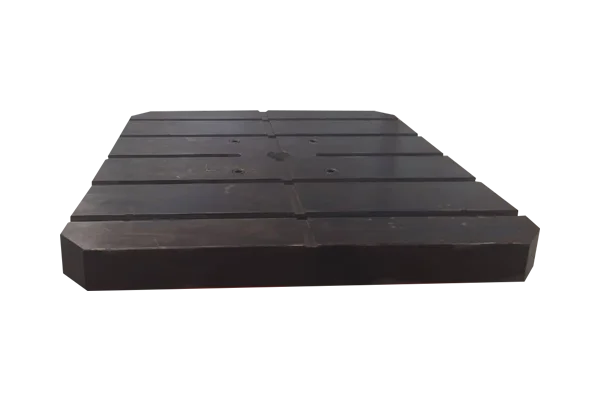
Rubber Moulded Collets In Oragadam are specialized components designed to combine the flexibility of rubber with the precision of collet mechanisms. This portfolio explores their unique attributes, applications across industries, benefits, and technological advancements shaping their evolution.
Introduction to Rubber Moulded Collets
Rubber moulded collets represent a fusion of rubber’s elasticity and collet’s precision, offering a versatile solution for securely gripping tools or workpieces. These collets are engineered to provide a cushioned grip, ideal for delicate materials and applications requiring vibration damping.
Key Features and Design Innovations
- Rubber Compounds: Utilization of specialized rubber compounds tailored for specific applications, balancing grip strength with resilience.
- Precision Engineering: Integration of precise collet mechanisms ensures consistent clamping force and dimensional accuracy.
- Vibration Damping: Rubber moulded collets absorb vibrations, reducing tool wear and enhancing surface finish quality.
- Temperature Resistance: Enhanced rubber formulations withstand varying temperatures encountered in machining environments.
Advantages and Benefits
- Enhanced Grip: Rubber moulded collets provide a secure grip on irregularly shaped or delicate workpieces, minimizing slippage.
- Vibration Reduction: Effective damping of vibrations improves machining stability and prolongs tool life.
- Flexibility: Ability to adapt to different workpiece geometries and materials enhances versatility in manufacturing processes.
- Cost Efficiency: Reduced tool replacement and maintenance costs due to improved tool longevity and part quality.
Applications Across Industries
- Precision Machining: Critical for micro-machining tasks where precision and surface finish quality are paramount.
- Electronics Manufacturing: Used in PCB assembly, semiconductor fabrication, and electronic component handling.
- Medical Device Production: Essential for manufacturing surgical instruments and medical implants requiring gentle handling.
- Automotive Industry: Applications include machining of rubber components, engine parts, and assembly line operations.
Technological Innovations and Trends
- Advanced Material Science: Development of novel rubber blends enhancing durability, chemical resistance, and performance.
- Industry 4.0 Integration: IoT-enabled collets monitoring performance metrics for predictive maintenance and process optimization.
- Additive Manufacturing: 3D printing of rubber moulded collets for customized designs and rapid prototyping capabilities.
- Smart Manufacturing: AI-driven algorithms optimizing collet performance based on real-time data analytics.
Case Studies and Success Stories
- Electronics Sector: Case study highlighting how rubber moulded collets improved yield rates and reduced defects in semiconductor manufacturing.
- Medical Industry: Success story of precision collets facilitating the production of complex medical device components with minimal material waste.
- Automotive Applications: Application of vibration-damping collets enhancing production efficiency and part quality in automotive assembly.
Future Outlook and Expert Insights
Industry experts anticipate continued advancements in rubber moulded collet technology, driven by demands for higher efficiency, precision, and sustainability. Emerging trends such as smart materials and green manufacturing practices will shape the future development and adoption of these innovative components.
Conclusion
Rubber moulded collets embody the convergence of materials science and precision engineering, offering unparalleled benefits in various industrial applications. By leveraging their unique attributes and staying abreast of technological advancements, manufacturers can optimize production processes and achieve superior results in dynamic market environments.