Special Collets In Oragadam
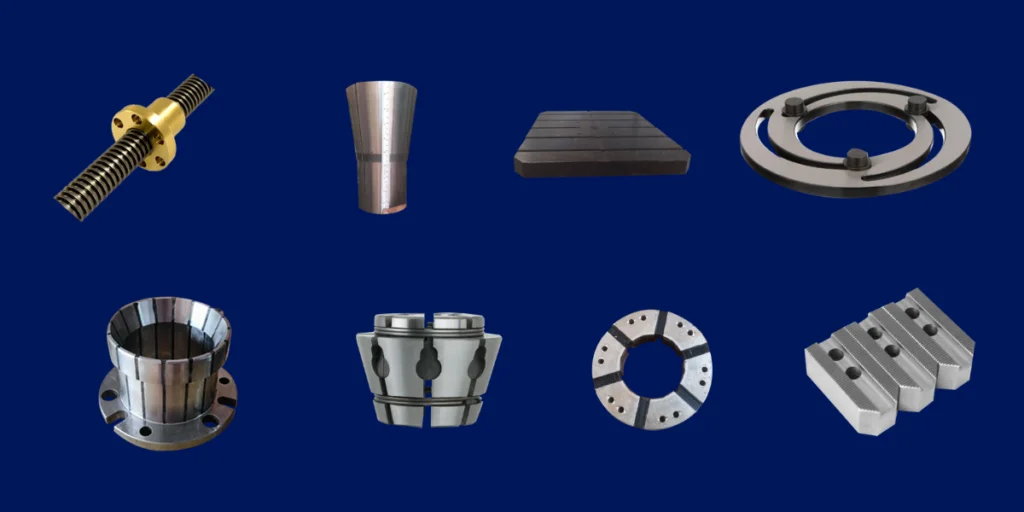
Special Collets In Oragadam In the world of machining, special collets play a critical role in ensuring precision and efficiency. These specialized tools are designed to hold workpieces and tools securely, reducing the risk of errors and improving the overall quality of the final product. This blog will explore what special collets are, their types, benefits, applications, and how to choose the right one for your needs.
Understanding Special Collets
Special collets are precision-engineered components used in various machining operations to hold tools or workpieces firmly in place. Unlike standard collets, special collets are designed to meet specific requirements or to handle unique shapes and sizes that conventional collets cannot accommodate.
Key Features of Special Collets
- Custom Fit: Special collets are designed to fit specific tools or workpieces, ensuring a perfect grip and reducing the chances of slippage.
- High Precision: These collets provide superior accuracy, which is essential for high-precision machining tasks.
- Durability: Made from high-quality materials, special collets can withstand the rigorous demands of machining operations.
Advantages of Special Collets
- Improved Accuracy: The custom fit of special collets ensures that tools and workpieces are held with high precision, reducing the likelihood of errors.
- Increased Efficiency: By securely holding tools and workpieces, special collets reduce setup times and increase machining efficiency.
- Versatility: These collets can be designed to hold a wide range of tools and workpieces, making them suitable for various applications.
- Enhanced Surface Finish: The secure grip provided by special collets helps achieve a better surface finish on machined parts.
- Cost Savings: The precision and efficiency provided by special collets can lead to significant cost savings in the long run.
Types of Special Collets
There are several types of special collets, each designed for specific applications:
- Special Shaped Collets: These collets are designed to hold workpieces with non-standard shapes, such as squares, hexagons, or other irregular shapes.
- Multi-Spindle Collets: Used in multi-spindle machines, these collets can hold multiple tools or workpieces simultaneously, increasing productivity.
- High-Speed Collets: Designed for high-speed machining operations, these collets provide a secure grip even at high rotational speeds.
- Micro Collets: Used for holding very small tools or workpieces, micro collets are essential for precision tasks in industries like electronics and medical device manufacturing.
- Adjustable Collets: These collets can be adjusted to hold different sizes of tools or workpieces, offering flexibility in machining operations.
Applications of Special Collets
Special collets are used in a wide range of industries due to their precision and versatility:
- Aerospace Industry: Used in the production of high-precision components for aircraft and spacecraft, where accuracy and reliability are critical.
- Automotive Industry: Essential for manufacturing engine components, transmission parts, and other critical automotive parts.
- Medical Device Manufacturing: Crucial in the production of medical devices that require high precision and reliability.
- Electronics Industry: Used in the manufacturing of electronic components, such as circuit boards and connectors.
- General Machining: Applicable in various general machining tasks, from milling and turning to drilling and grinding.
Choosing the Right Special Collet
Selecting the right special collet involves considering several factors:
- Material Compatibility: Ensure the collet material is compatible with the tool or workpiece material to prevent damage and ensure a secure grip.
- Size and Shape: Choose a collet that matches the size and shape of the tool or workpiece you are working with.
- Type of Machining: Different machining operations may require different types of collets. Consider the specific needs of your operation.
- Load and Stress Factors: Ensure the collet can withstand the operational loads and stresses without deforming or failing.
Innovations in Special Collets
Technological advancements have led to significant innovations in the design and manufacturing of special collets:
- Advanced Materials: The use of high-strength alloys and composite materials enhances the performance and durability of special collets.
- Precision Manufacturing: Modern manufacturing techniques, such as CNC machining, allow for the production of collets with extremely tight tolerances, improving their precision and reliability.
- Custom Designs: The ability to design and manufacture custom collets tailored to specific applications provides even greater flexibility and performance.
Maintenance and Care for Special Collets
To ensure the longevity and performance of special collets, proper maintenance and care are essential:
- Regular Cleaning: Keep collets clean to prevent debris from affecting their clamping ability.
- Inspection for Wear: Regularly inspect collets for signs of wear or damage and replace them as needed to maintain accuracy.
- Proper Storage: Store collets in a clean, dry environment to prevent rust and corrosion.
- Lubrication: Apply a light coat of lubricant to moving parts to reduce friction and wear.
Conclusion
Special collets are indispensable tools in modern machining, offering unparalleled precision, flexibility, and durability. By understanding their features, advantages, and applications, and by selecting the right type for your needs, you can significantly enhance your machining processes. With ongoing innovations in materials and manufacturing techniques, special collets continue to evolve, providing even greater capabilities for high-precision machining tasks.